Rigorous, quality aftersales seen as key to BMW Brilliance's success
Dubbed "Superb Techniques and Trustworthy Choice", BMW's interactive and in-depth workshop on its body and painting techniques demonstrated its strengths in the aftersales service and continuous efforts in improving customer satisfaction.
The German brand, as the first premium automaker launched an aftersales service brand, showed to a group of media the rigorous process in the body and painting, and aftersales services' focus on the safety, superb techniques, and environmental protection in its training center in Beijing on Dec 4.
"High-quality aftersales service is the key to BMW's differentiation from the other luxury auto brands, and also one of the three core competitiveness of BMW, together with a passionate brand and attractive lineups" said Clifford Kang, vice-president of aftersales at BMW Brilliance Automotive Co Ltd.
BMW technicians shared their insights at the interaction session. Photos Provided to China Daily |
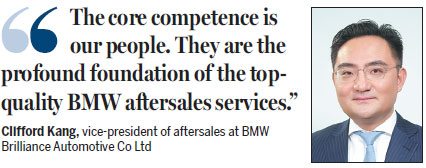
The body structures of all-new BMW 7 Series and i3 are displayed to show the use of aluminum and carbon fiber. |
"BMW aftersales services have been leading in the premium segment and became the benchmark for its quality, value, care, and convenience," he told the reporter.
The repairing service, including body work and painting, represents the superior level of BMW aftersales service. The insights in the changing consumers' demands and staying ahead of the era helps BMW maintain its pole position among the premium auto brands.
Following the BMW Group's Strategy Number One > Next, BMW aftersales services will continue to transform from "a luxury car manufacturer" to "a high-end individual mobility service provider" in aftersales service. In the future, BMW will win the trust of every customer with high-quality service and innovative service model.
Kang said: "Winning the trust of our customers is the cornerstone of BMW's competitiveness in the luxury car aftermarket based on high quality service and customer orientation.
"The core competence is our people. They are the profound foundation of the top-quality BMW aftersales services."
More than 6,000 professional body and painting technicians are serving the customers throughout the country, and meeting their high expectations in quality, according to company data.
A qualified BMW technician is required for at least 3 years of systematic learning and practice, including more than 1,000 hours of study, more than 10,000 operations, and twice-yearly rigorous certification.
BMW has four training centers and 15 training bases throughout the country, providing powerful knowledge support for aftersales service teams. The total training sessions have accumulated to 470,000 times.
Exquisite body service techniques
"We have been continuously focusing on the customers' demands, which are the safety, superb techniques, and environmental friendly," Kang noted.
As the world's leading luxury car brand, BMW always puts customer safety in the first place.
The target of BMW's body work is to keep the vehicle always as rigid and safe as just rolled off from the plant. BMW's superb body work techniques repair a wide range of body structures for a robust connection and thus restore the body's safety performance.
The body repairing process is so strict that BMW technicians must follow the world's consistent processes and parameters, no matter in replacing a body side, or installing a bolt.
Regardless of how a vehicle might deform in an accident, BMW body repairing will restore the shape and size to the state at the factory, and with a tolerance less than 1 mm from any angle.
Flawless painting
BMW took the lead in implementing-waterborne paints in China since 2005, to minimize the environmental impacts. More than 70 percent ingredients of BMW's ColorSystem is water, which reduces emissions by more than 3,500 tons of volatile organic compounds every year, when compared with conventional paints that have up to 84 percent of VOC. It's equivalent to planting half a million trees, according to the company.
The use of dust-free dry grinding instead of conventional water blasting in BMW painting operations reduces about annual 20,000 tons of sewage. It's equivalent to 235,000 people's water consumption per day, besides protecting 3,000 painting technicians from harm. In the drying process, BMW employs electric or infrared instead of diesel, reducing carbon emissions nearly 20,000 tons each year. The BMW standard painting process consists of 10 major processes, more than 30 minor processes, including fine processes of blading coating, sanding and painting. Operated by certified professionals, about 20 tools and equipment and more than 50 specialized materials were used to ensure the perfect match with the original exterior color.
Innovative service models
BMW Aftersales Services will continue to bring convenience and care to more than 3.2 million Chinese Bimmers through innovative models.
The aftersales service team actively involved in the research and development of new models, together with the constantly upgraded vehicle technology, to provide customers with a more comprehensive safety.
Accident Assistant is already deployed in the all-new BMW 5 Series Li, and will be equipped on other models in the future. Also, more than 3,200 mobility cars have been provided to the customers with mobility services. The vehicles have served more than 80,000 users, and the cumulative service days total 420,000 days. The accelerated digitization reflects the forward-looking and innovative BMW service. For example, the BMW Connected app is offering a wide range of functions, including service reserving, vehicle pick-up and drop-off, roadside assistance, and illegal violation inquiries. Thanks to its more convenient and high-quality aftersales experience, BMW Connected app now has more than 500,000 registered users.
haoyan@chinadaily.com.cn
(China Daily 12/11/2017 page19)