The making of an erhu
Python skin and carefully aged wood are essential to this ancient craft
The erhu, a traditional Chinese musical instrument that is sometimes known by Westerners as the Chinese fiddle, is an integral part of life in Jiangyin, Jiangsu province.
Strolling through the city, one will often encounter people of all ages playing this instrument. During special occasions, the unique sounds from an erhu often accompany the scenes of jubilation.
The origins of the erhu can be found in its name. In Chinese, the first character "er", which means "two", refers to the two strings on the instrument, while the second character "hu" refers to its place among a family of instruments dubbed the "huqin" which the Hu people are known to use. Hu is generic term used to refer to the nomadic ethnic groups living in the northern and western regions of China in ancient times.
The instrument is widely believed to have originated during the Tang Dynasty (AD 618-907) as it was often mentioned in poems and other literature, though the appearance of the instrument might not be the same as it is now.
The modern erhu consists of a long neck, two tuning pegs and a small sound box. Two strings run from the peg to the end of the sound box. The side of the box where the strings are located is traditionally covered with python skin. The bow used with the erhu is usually a bamboo stick that is fitted with horse hair.
"To make a good erhu is no easy job. There are about 200 steps in the whole crafting process," says Kong Zhenping, the owner of an erhu workshop in Jiangyin.
Kong, 48, started making erhus in 1990. He later founded his own workshop in 1998 and has since been selling his handmade erhus to foreign and domestic customers. Kong has about a dozen staff in his workshop, including a professional tuner who tests each erhu before it can be put up for sale.
According to Kong, the price of an erhu ranges between several hundreds and tens of thousands of yuan. He notes that a decent one will cost more than 1,000 yuan ($150).
"An erhu of this price will have good tuning and quality for those who want to learn the instrument seriously," says Kong.
Kong says that it takes four to five days to make an erhu in his workshop. One of the most essential elements is the wood used to craft the instrument as it determines the type of sound produced. In order to achieve better stability, the raw wood, usually sandalwood or rosewood, has to be dried for more than a year so that it will not contract during the crafting process.
"Generally speaking, the older the wood, the better it is," explains Kong. "Usually, you can tell the age of the wood based on its color. Wood turns darker with time."
The process of gluing the python skin to the sound box is also an important one. Much care must be taken to ensure that the skin is not too loose or overly stretched. The last step in making an erhu is the application of paint and wax which enhances durability and gives it a glossy appearance.
"I didn't play the erhu when I first started making them, but its tradition in Jiangyin made me feel close to it," recalls Kong.
"Back then it was just a job opportunity. I never knew it would take me this far."
xingyi@chinadaily.com.cn
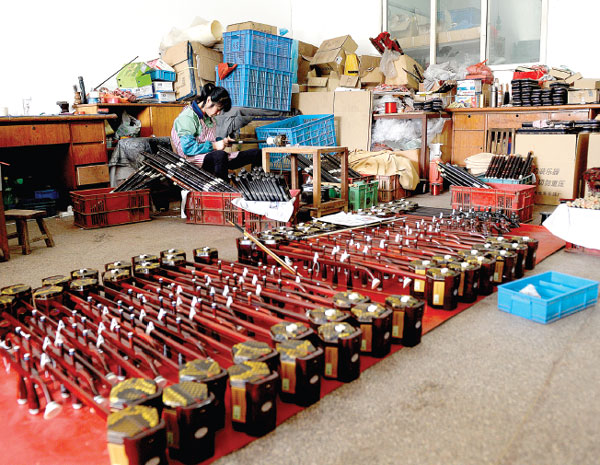
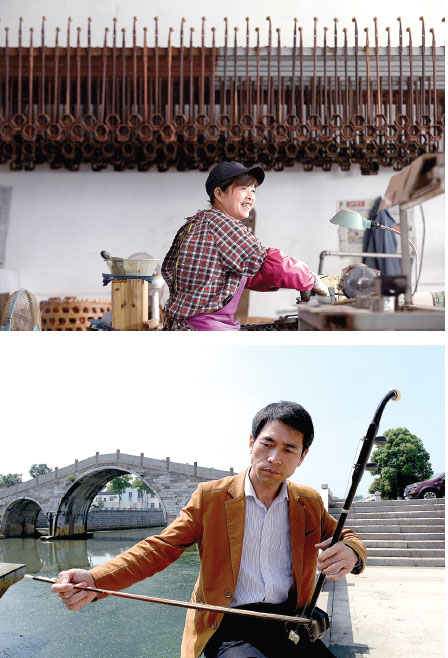
Strolling through Jiangyin, one will often encounter people of all ages playing erhu. The making of this musical instrument is a traditional craft still alive today. photos by wei xiaohao / China Daily |
(China Daily 07/15/2016 page42)