Shandong facility gets the most out of old NEV batteries
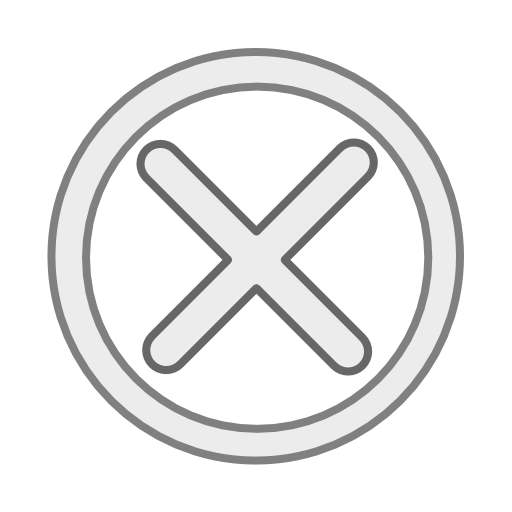
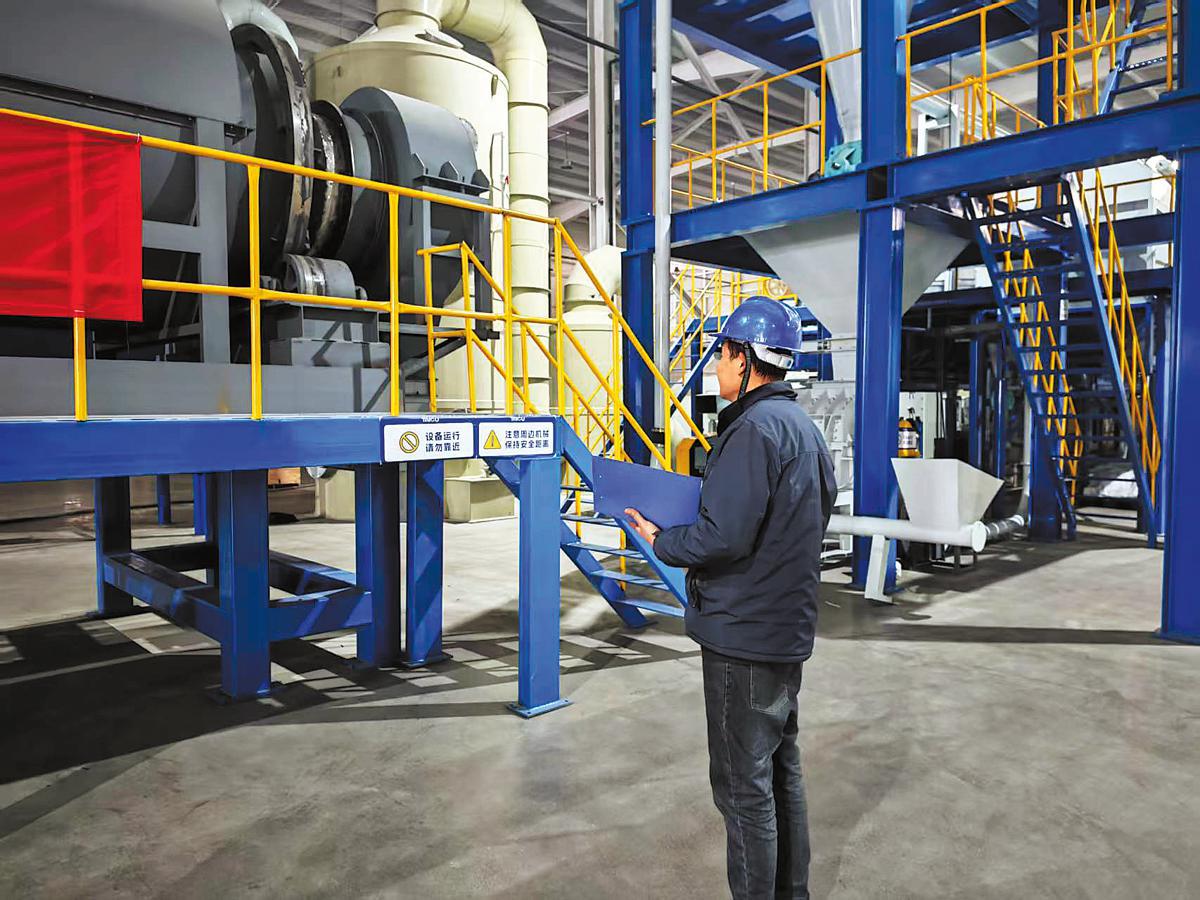
At a battery recycling facility in Hedong district of Linyi, Shandong province, the used batteries from new energy vehicles are processed into lithium, copper and aluminum powder in just over 10 minutes. This project, initiated at the end of last year, aims to transform old batteries into valuable resources.
As China steers toward a carbon dioxide peak before 2030 and carbon neutrality before 2060, the new energy vehicle sector faces a rapid expansion. However, the recycling of used batteries, laden with heavy metals and environmental risks, presents a crucial challenge.
"In our city, new energy vehicles accounted for nearly half of all car sales last year, with a rapid growth of 40 percent, indicating the battery recycling facility in the district has a big market potential," said Sun Quancheng, a senior official of Hedong district.
The facility incorporates a sophisticated four-stage crushing process and three rounds of grinding and sorting into separate battery casings, black powder, copper powder and aluminum powder. Notably, it achieves a recycling rate that surpasses the industry average by 5 percentage points.
Cui Guoshi, the deputy general manager of Shandong Taigu Jiantou New Materials Co, which operates the facility, likens the final sorting process to "winnowing wheat", where heavier copper and aluminum particles settle while lighter battery powder is carried upward by airflow.
"This meticulous sorting results in a battery powder with less than one percent copper and aluminum content, enhancing its quality for reuse," said Cui.
The extracted battery powder contains nickel, cobalt and lithium — critical components for lithium-ion batteries.
"After further refinement by hydrometallurgical technology, these metals like nickel and cobalt can be reused in producing new batteries," said Xia Mingyuan, the company's general manager.
Traditional battery recycling methods require at least seven days of discharge treatment before crushing — a process prone to creating pollution.
To address this, the facility in Hedong district has developed an innovative system that crushes charged batteries safely by using nitrogen protection and instant pyrolysis, making recycling faster and cleaner.
Wang Delong, another deputy general manager at the company, said that the facility's system continuously injects nitrogen into the processing equipment, with sensors automatically adjusting levels to maintain oxygen concentration below 5 percent. "This effectively prevents battery combustion," he said.
Although retired EV batteries often retain 70-80 percent of their capacity, enabling secondary uses like electric tricycles and tools, their ultimate dismantling and recycling are imperative.
"Previously, these batteries in Shandong had to be transported to recycling facilities in southern China for crushing and reprocessing, incurring substantial costs and safety risks during transit," said Yang Yang, deputy secretary-general of the Shandong power battery recycling association.
Bolstered by robust local government support, the project was integrated into Shandong's green, low-carbon, high-quality development agenda, facilitating swift approval and production within a mere three months in Linyi.
Plans are underway to introduce five additional production lines for future expansion alongside the existing operational dry-process line.
Upon reaching full capacity, the project is poised to annually recycle 40,000 metric tons of lithium batteries, setting a benchmark for sustainable battery management in alignment with China's green transition.
zhaoruixue@chinadaily.com.cn
- Shandong facility gets the most out of old NEV batteries
- Chinese doctors provide smiles to children born with cleft lip in Tanzania
- AI-powered hospitals to offer faster, expanded care
- Public health system to be enhanced
- Travelers choose rural escapes for May Day break
- Runner carries hope for reunited families