Buoyant exporters face post-pandemic blues
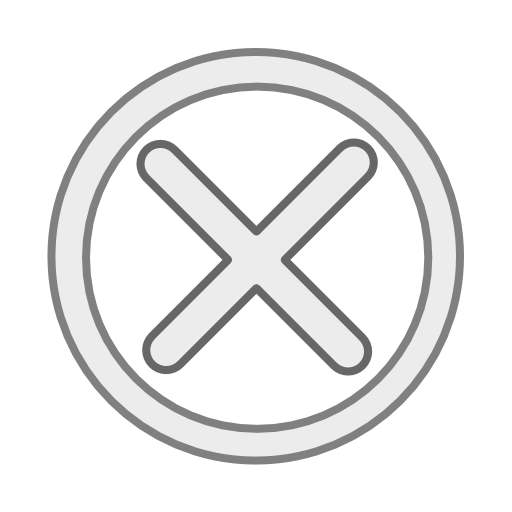
Mainland electronics makers need to strengthen product innovation, explore untapped markets and upgrade digitalization transformation to stay on top once the crisis eases. Chai Hua reports from Shenzhen.
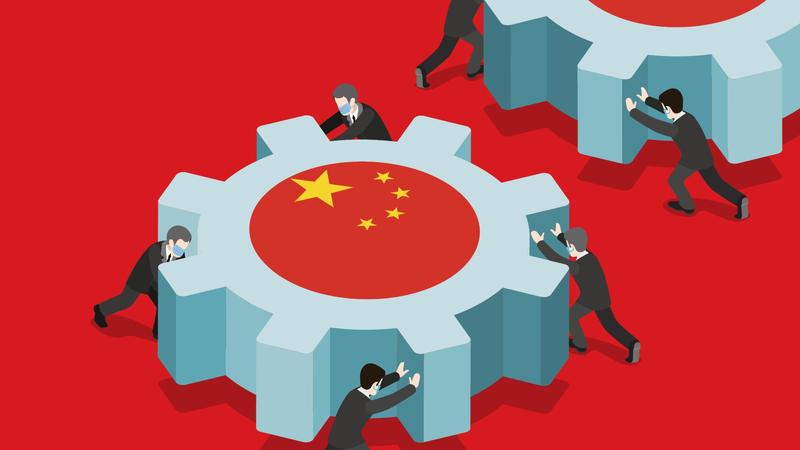
A record surge in Chinese exports last year amid the COVID-19 pandemic was out of this world, reflecting the strength of the nation's supply chain.
The electronics sector stole the show with factories in Guangdong province — China's manufacturing hub — pushing ahead at full steam to expand production capacity to meet global consumers' needs as they remained confined to their homes.
However, rising labor and logistics costs accompanied the roaring production, and sparked concerns about a rebound in competition after the coronavirus wanes.
Their solution to long-term growth in the post-pandemic era is to proactively strengthen product innovation, explore untapped markets and upgrade digitalization transformation.
As the Chinese mainland strives to contain the pandemic and restore production to that of its heyday, it has boosted export orders, which were led by robust sales of pandemic control and electronic gadgets.
Total exports in 2020 hit a historic high of 17.93 trillion yuan (US$2.77 trillion) — up 4 percent on a yearly basis — according to official data released on Jan 14.
Guangdong's exports rose to a record 4.35 trillion yuan in 2020, according to Guangdong Customs statistics.
Besides the commitment to pandemic prevention and control, the rebound exemplified the comprehensiveness of the mainland's supply and industrial chains, which guaranteed the continued running of manufacturing and the economy, said Cao Zhongxiong, executive director of the New Economy Research Institute at Shenzhen-based think tank, the China Development Institute.
Watch out for idle capacity
But he noted that export orders have been chalked up due to the continued suspension of production or under-production in other countries and regions amid the pandemic. Thus, the likelihood of competitors returning in droves and shrinking international demand is real as the pandemic eases, he warned.
Manufacturers that have expanded production to cope with rising demand should watch out for idle capacity in the long term, said Cao.
Factory owner Lu Hang's Shenzhen plant has been making and exporting mice, keyboards and numerous types of computer gadgets for more than three decades, but last year was the busiest.
With many people working from home to help curb the coronavirus, the demand for computer equipment was huge. To meet mounting orders from overseas markets, Lu has expanded the factory's production capacity tenfold and hired about 1,000 workers last year.
Despite the expansion, he kept a clear head in anticipation of a drop in orders when the global pandemic is brought under control. "I've prepared new products and we're exploring new markets," he said. "I expect our revenue to go up by a further 50 percent this year regardless of the pandemic situation."
To avoid idle production capacity in the future, Lu has been tapping the domestic market since the annual "Double 11" shopping spree on Nov 11 last year.
Quality offers prosperity
Many mainland exporters are turning to consumers at home as the central government is pushing economic growth through the "dual-circulation" development paradigm, in which the domestic market is the mainstay, with the domestic and foreign markets complementing each other.
Whether it's for a domestic or international market, Lu is consistent with high-quality products.
"The revenue of both low-end and high-end products is booming as the entire electronics market is flourishing. But only technology innovation and top-notch brands could offer long-term prosperity," he said.
What worries Lu is the soaring cost of labor. He said although workers' wages have gone up by half, it's still difficult to find enough staff.
Shenzhen-based TCL China Star Optoelectronics Technology is also spreading its wings.
The company put a new production line with a monthly output of 90,000 display panels into operation in the fourth quarter of last year, while its purchase of Samsung's factories in Suzhou is expected to add capacity by another 120,000 units each month upon completion.
TCL China Star's export shipments increased by 7 percent in 2020 and annual revenue growth exceeded 35 percent.
The display panel maker believes the new factories will continue to play a key role in the post-pandemic era. It aims to seize the new opportunities in the vehicle market and the production of 12-inch chips — the industry's latest development trend.
A manager said the company plans to strengthen the production transformation process by establishing a new model of cloud-based coordinate intelligent manufacturing, connecting its factories across the country and partners along the industry upstream and downstream.
"From our experiences and observations, our customers in the Bay Area are very adaptive and have been quick to deploy new technologies and business models," said Henry Ko Hok-han, managing director of digital freight forwarder Flexport Asia.
The Bay Area has the most complete supply chain and a superior digital infrastructure to support the adoption of new technologies and business models, Ko said. It's crucial for companies to be more agile and resilient in any crisis or when facing uncertainties in the post-COVID-19 era.
New technologies beneficial
The global freight forwarder upgraded its digital platform last year, empowering users to spend about 40 percent less time in locating shipments and 60 percent less time in completing shipping documentation.
These features are beneficial for exporters who faced container shortages and rising costs in the second half of last year.
According to Ko, the average cost of shipping a standard 40-feet container to the United States has risen two to three times, and that to Europe by up to four times, as a result of growing shipping volumes and the shortage of manpower at the destination ports.
Only 1 container returns to the mainland out of 3 to 3.5 containers shipped overseas, he said.
When the goods arrive at ports, it normally takes three to five days for truckers to move the shipments out for inland transportation. Due to the congestion and lack of labor, the transportation could now take several weeks.
Ko suggested that manufacturers and exporters reduce their transaction costs by improving efficiency instead of just focusing on the freight-related costs, diversifying their supply and selling bases, and leveraging the opportunities created by new regional trade pacts, such as the Regional Comprehensive Economic Partnership accord and the Comprehensive Agreement on Investment between China and the European Union.
- Experts urge stronger civil aviation legislation, cultivation of legal talents
- Henry C. Lee praises women's rising role in forensic science
- China's national college entrance exam begins
- China issues yellow alert for rainstorms
- 78,900 students across Beijing sit the gaokao
- Chinese, American youths bridge cultures through dance