The process of prestige
Guangdong gauze, once a luxury reserved for the wealthy, can take months to make due to its time-consuming production and the use of natural materials, Yang Feiyue reports.
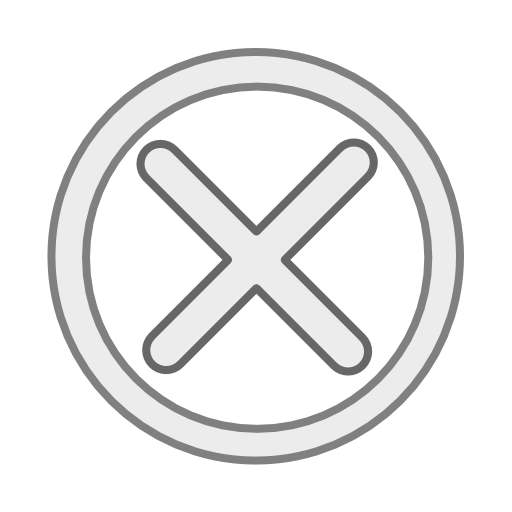
If you wear a garment made of xiangyunsha, people in Shunde district in Foshan, Guangdong province, might joke that you're draped in a layer of "soft gold".
While it may sound like an exaggeration, the statement about xiangyunsha (literally "fragrant cloud gauze"), also known as gambiered Guangdong gauze, reflects the fabric's historical prestige. Dating back to the Song Dynasty (960-1279), it was once a luxury only the wealthy could afford.
Made from premium mulberry silk, the fabric undergoes a complex, laborintensive production process that includes repetitive dyeing with natural plant extracts, sun-drying, and coating with river mud.
"It can take months to complete with the traditional technique, resulting in a lightweight, breathable and natural antibacterial fabric," says Ouyang Fengting, 60, who has more than a decade of experience in the craft, which was listed as a national intangible cultural heritage in 2008.
The heavy reliance on skilled artisans, coupled with limited raw materials and a time-consuming production process, leads to small quantities of xiangyunsha, contributing to its premium price.
"The sun-drying stage must be done under intense sunlight. It takes three to four years to train a skilled artisan," she explains.
The distinctive characteristics of the fabric also resulted in its export to regions such as Europe, the United States and Southeast Asia during the 1930s, according to local historical documents.
While modern technology has, in some aspects, streamlined production process and reduced costs, the creation of Guangdong gauze still largely relies on laborious and meticulous manual work.
"Xiangyunsha can stand the test of time. As years pass, it becomes glossier, softer and more luminous," says Ouyang, who was born and raised in Shunde.
The colors are different from those of nylon or synthetic fabrics and have a deeper, more ancient tint, she adds.
There has been a recent resurgence in the popularity of traditional Chinese attire, with xiangyunsha making a comeback after being nearly forgotten in the 1970s and '80s, a period marked by lower living standards and the prevalence of modern fabrics.
Ouyang has noticed the expanding market demand. Orders in January surged by 50 percent over the same period last year. "Our products are in great demand. We are looking for employees to fill the gap," she says.
Nature's gift
Under bright light, the black side of the fabric gives off a metallic luster while the reddish-brown side takes on a cracking pattern that changes with time.
"The craft of creating xiangyunsha relies on five indispensable natural elements: mulberry silk, natural dyestuff, river mud, grass fields and sunlight. Thus, it is often referred to as 'a gift from nature'," Ouyang explains.
Located in the center of the Pearl River Delta, Shunde is home to an intricate network of rivers, with fishponds scattered across the landscape. Ancient fishermen discovered that soaking their fishing nets in yam sap made them more durable and resilient.
An accidental discovery was made — when their clothes were stained with sap and river mud, they became cooler and more durable. This serendipitous find gradually evolved into a unique dyeing technique, which was ingeniously applied to silk.
Ouyang's interest in the fabric developed during her childhood, as her family cherished garments made from this material.
During the summer when air conditioning was rare, wearing xiangyunsha was incredibly comfortable, she recalls.
However, it wasn't until she worked as an accountant that she could afford the garments sold in shops.
"I was shocked when I saw the rich colors and styles of the garments on display," she says.
From that moment, her fascination with xiangyunsha deepened, and her frequent visits to the shops eventually led her to meet Liang Zhu, a shop owner and a national-level inheritor of xiangyunsha dyeing and finishing techniques.
Through their interactions, Ouyang realized that the sun-drying process is not only complex and labor-intensive, but also requires artisans to endure long hours of exposure to the sun.
"It was a hard job with little pay," she says.
After learning that fewer people were willing to enter the tough trade, she shifted her career trajectory and dedicated herself to preserving the craft alongside Liang in 2014.
She followed him in every step of the craft and visited other artisans to learn from their experience.
The dyeing process involves soaking the fabric in yam extract and then drying it in the sun. This step is repeated multiple times to achieve the desired color and texture.
Following the dyeing process, the fabric is laid out on the grass and coated with mud infused with iron-rich minerals that interact with the tannins in the yam dye, resulting in a lustrous, dark surface on one side of the fabric. This treatment also boosts the fabric's resilience and water resistance.
It is then dried in the sun to set the color. The sun-drying process is repeated multiple times, alternating with additional applications of yam dye and mud.
After this, the fabric is thoroughly washed to remove excess mud and dye. It is then dried again and smoothed out.
After years of enjoying manicures, Ouyang now cuts her nails short, as the yam sap often gets stuck under her nails.
Growing allure
As she mastered the craft, Ouyang's understanding of the fabric's allure deepened.
"The base material of xiangyunsha is mulberry silk, a protein fiber known for its breathability, softness and comfort, while using yam sap not only imparts a unique color to the fabric, but also endows it with medicinal properties such as hemostatic and antiallergic effects," she explains.
When she traveled to major cities like Shanghai and Jiangsu province's Suzhou, Ouyang found widespread misunderstanding and misinformation about xiangyunsha.
"Many people don't know what authentic, high-quality xiangyunsha is," she says.
During the early 2010s, the market saw a surge in imitations as machine production enabled the creation of xiangyunsha within a mere three to four days. These low-cost, low-quality products severely affected traditional workshops.
Ouyang realized it was imperative to preserve xiangyunsha through branding and standardization.
In 2018, she and her mentor Liang cofounded the brand Tangxian.
"We focus on fabric production, with 90 percent of the materials made using traditional methods," she says, adding that her company strictly follows the ancient dyeing process — three steams, nine boils, and being sun-dried 18 times.
The brand has developed over 50 types of fabric based on traditional techniques, with products ranging from clothing and shoes to accessories like hats and handbags.
Her company also developed a tracing system that records each step of the fabric's production process.
"By scanning a QR code, buyers can see exactly how their xiangyunsha was made — down to the weather report on the days it was sun-dried and the specific location where the drying took place," she says.
As an increasing number of young people appreciated the craft, she began livestreaming in 2021 on Douyin, where she shares details of the craft. The company landed big orders, with the largest worth more than 1 million yuan ($138,000).
"My fan base is growing, too. Many drop by from all over the country," she says.
Chen Shaofeng, a professor from Peking University, says the Tangxian brand has effectively promoted the integration of the fabric with modern life, products and aesthetics.
He considers it a good move to carry forward xiangyunsha, which is "one of the few silk fabrics in the world dyed using purely natural ingredients".
Wang Shousong, executive director of the EU Culture Administration, is impressed by xiangyunsha and the culture behind it.
"It carries forward China's exceptional tradition of handmade artistry, showcasing the essence of Chinese history, culture and art through embroidered patterns that reflect its depth and richness," Wang says.
Ouyang's years of experience have underscored the significance of grasping the contemporary market's requirements for xiangyunsha.
Despite this, she says it must not compromise the original quality of traditional craftsmanship.
"The charm of xiangyunsha lies in its handmade craftsmanship, the use of plant-based dyes, and absence of chemical additives," she says.
Once these elements are altered, the fabric's uniqueness and exclusivity will be lost, she adds.
Ouyang and her team are developing a wider range of patterns and exploring techniques like fruit and plant dyeing.
"There's still room to grow," she says.
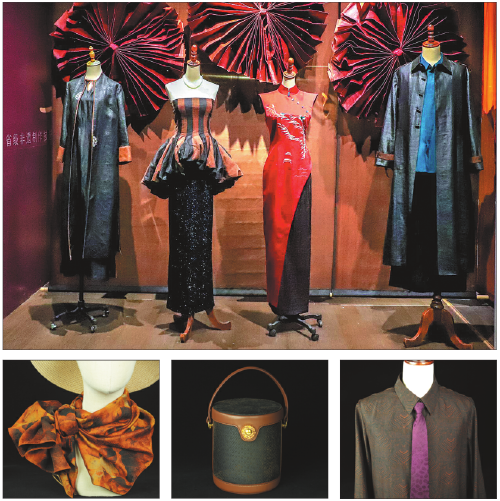
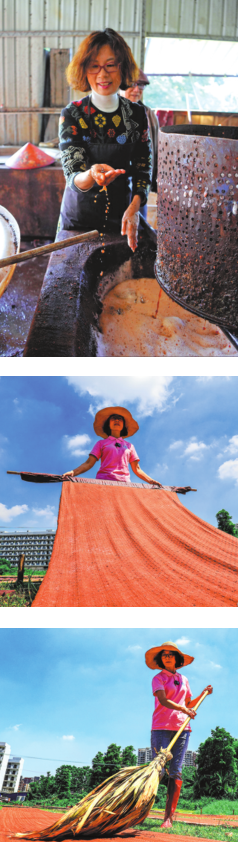
Today's Top News
- China approves some rare earth export applications
- Sino-US talks expected to help build up consensus
- National Guard arrives in Los Angeles amid immigration protests
- Nation's trade in services accelerating
- Navigating Sino-US trade ties through dialogue
- Former senior military official Xu Qiliang's remains cremated