A year of supply chain woes, late ships and worker shortages
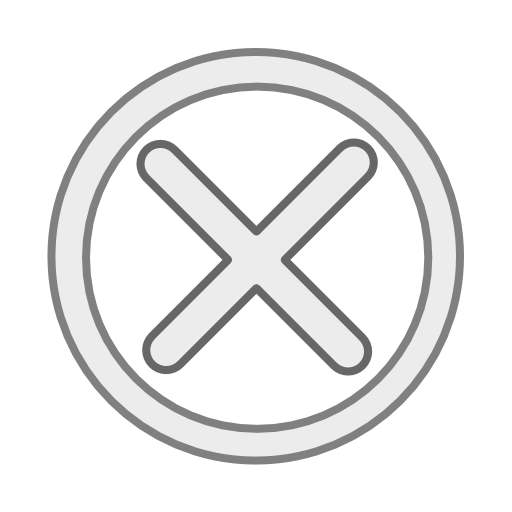
This is the fourth month that Lee has been waiting for a package from China. His family in China sent him the package in September, and it was supposed to arrive in November.
There are winter clothes for Lee's children in the package. Lee thought it would arrive before winter.
"I ended up buying winter clothes for my kids in local shops," Lee told China Daily. "I have asked the delivery company, and they said that they could not confirm the date of delivery. I may still have to wait a long time."
Meanwhile, container ships waiting offshore in Los Angeles and Long Beach are piling up. The logjam hit a peak of 93 container ships offshore on Nov 23, according to the Marine Exchange of Southern California, which monitors ship movements in the area.
Less than half of ships worldwide arrived on time this year, and ship delays continued to add more than a week to delivery times-compared with about four days in 2018 and 2019, according to Oxford Economics.
"It took 40 days for our ships to travel from China to the US, but now they need to travel for at least 60 days," said Junbo Li, a representative of an international logistic company, to China Daily.
It also takes longer to get goods off cargo ships and onto store shelves and houses due to soaring costs and shortages of dock workers and truck drivers.
Containers piled up
"Containers are piling up on the dock and we need more truck drivers to deliver goods," he said.
The current driver shortage in the United States has risen to 80,000-an all-time high for the industry, according to an American Trucking Associations report released in October. The association estimated that the shortage could double by 2030 as more drivers retire.
"Increased demand for freight, pandemic-related challenges from early retirements, closed driving schools and DMVs, and other pressures are really pushing up demand for drives and subsequently the shortage," said Bob Costello, chief economist and senior vice-president of the ATA, in the report.
Patrick Penfield, professor at Syracuse University's Whitman School of Management, said the COVID-19 pandemic has posed significant challenges and changes for global supply chains.
"The pandemic really kind of changed everything. It changed how we order things, it changed how we bought things, it causes a lot of stress," said Penfield to China Daily. "The demand pattern shifted."
Supply chain problems stem from a number of factors, including increasing demand for goods and factory shutdowns abroad.
Factories and retailers in Western economies that have largely emerged from lockdowns are eager to obtain raw materials, finished goods and components from longtime suppliers in Asia and elsewhere.
"People had more money because they weren't going out, they weren't traveling. That caused a lot of stress to the supply chain because people were buying more things," Penfield said. "And then you need more things. If you have an office at home, you need a camera, you need a laptop."
But the pandemic had caused many countries in Asia to shut down its factories, slowing or temporarily stopping the flow of raw material and finished goods, constricting their ability to meet demand as a result.
Pandemic-related factory closures in Malaysia this year have hit chip supplies of German carmakers in a semiconductor market already battered by outages in Texas and Japan. According to a Wall Street Journal report, supply chain specialists said a lockdown in Vietnam has created problems for Australian importers.
If Omicron hits supply chains, the impact on Asia's gross domestic product is likely to be a fall of 1.6 percentage points next year, Oxford Economics said. Climate change is also threatening supply chains. A rise in the probability of severe weather events and disasters each year is damaging manufacturing facilities and other assets. Crop yields are likely to fall due to wildfires, droughts and pests.
The annual cost of disruptions to supply chains from natural disasters in US rose to $95 billion last year, according to a report by the National Centers for Environmental Information in September.
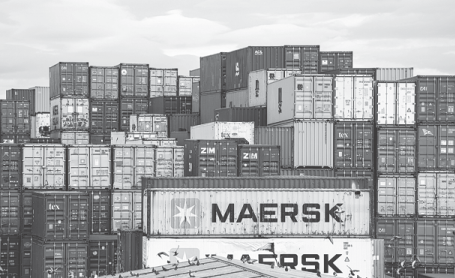
Today's Top News
- Trump's 50% tariff threat on EU goods draws rebuke
- Xi sends congratulatory letter to 20th Western China International Fair
- China to boost high-quality development in national development zones
- Xi extends condolences over death of former Vietnamese president
- Ukraine crisis a lesson for the West
- Autonomous networks driving the progress of telecom sector