A beautiful craft that refuses to die
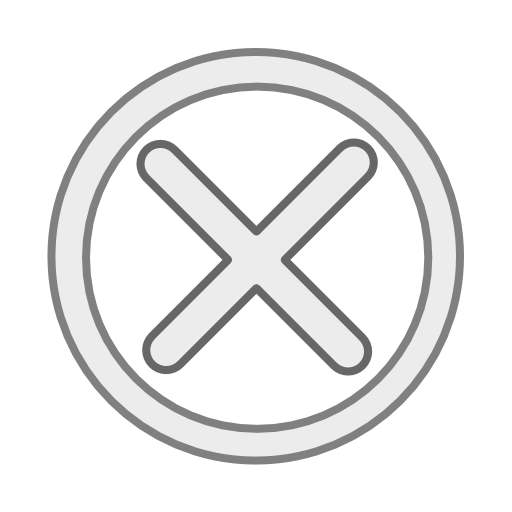
Above: Zhong Liansheng says Beijing Enamel Factory's products have a more modern touch. Left: Polishing is the fourth step of making an enamel vase. Photos by Jiang Dong / China Daily |
Commercial realities have caught up with an art form that is 600 years old
At dusk on a summer's day 12 years ago, Zhong Liansheng was cycling in Beijing with his young daughter straddled on the back of his bike. When they passed Longtan Lake in Dongcheng district, Zhong was mesmerized by the scene. The leaves and lotus flowers bathed in a twilight glow gave off a warm romantic air, perfected by a couple of wild ducks paddling gently by.
Moved by the beauty of the moment, Zhong, an artist, started to think about representing the warmth and romance in his work.
In 2001 his Dream in the Lotus Pool was presented in a collection of five enamel products: four bottles and a plate with the romantic moment burnished on the surface. In producing the work, he used radically new design techniques, resulting in a successful creation that has led the cloisonne craft in China in a new direction.
Zhong, 50, general manager of Beijing Enamel Factory Co Ltd, is the youngest China Arts and Crafts Master in enamel craftsmanship, an undertaking that has them laboring to help an ancient tradition survive and prosper in the modern age.
"We are making products not only in the traditional way, with the usual representations of luck, wealth and long life, but are working with themes that are closer to daily life and that have a more modern touch," Zhong says. "They also need to fulfill the demands of the market."
Enamel craft came to China about 600 years ago, but until the end of the Qing Dynasty (1644-1911), cloisonne ware was made for royal families only.
With the collapse of the Qing Dynasty, the craft's techniques breached the walls of the Forbidden City. But rather than flourishing in this new-found freedom, the craft, with many other crafts and arts, reached the brink of extinction over the following decades of conflict and as the cost of materials rose.
In the first years after the People's Republic of China was founded in 1949, people started saving the dwindling number of these treasures. In 1956, 42 private enamel factories emerged and formed Beijing Enamel Factory in Dongcheng district.
If the 40 years after 1911 had seemed to sound a death knell for the craft, in the 1950s and 1960s, thanks to Beijing Enamel Factory's efforts at preserving cloisonne techniques, it became clear that the craft was not yet ready to die.
Since the 1970s the factory has produced many enamel products for export to more than 100 countries and regions. In fact, 70 percent of the enamel products that left China in the 1970s and 80s were made at the Beijing Enamel Factory, which by the early 1990s employed more than 2,000 people.
Enamel techniques have continued to evolve, one example being the ceramic glaze color palette, which now boasts 60 hues, three times more than it used to.
"We can blend almost any color we want, and the skills and techniques are better than they have ever been," Zhong says.
Such improvement has not come about by accident. In 1977, the year China restored the national college entrance examinations, the factory opened a polytechnic school offering training in the craft.
"Before the school opened, apprentices learned from old crafts people," Zhong says. "Every craftsperson has a particular strong suit, so what students learned was limited, but the polytechnic school systemized and standardized the production process. That meant we could systematically learn traditional skills and patterns, and we could come up with new ones."
Zhong was one of the school's first students. He studied artistic design and practiced the most important skills. Three years later, he graduated and stayed at the school as an assistant teacher. Later he took part in production and created many new designs.
However, the craft faced yet another challenge. In the early 1990s, the development of the country's market economy put question marks over State-owned factories, and Beijing Enamel Factory was one of them.
"We produced mainly for export because at that time the domestic consumer market had not been developed. In the planned economy we took orders directly from a State-owned trading company and did not need to worry about orders. But in the 1990s things changed and we had to worry about the market."
Another challenge for the factory was that the market was awash with a lot of cheap, poor-quality cloisonne ware.
"It was the most difficult period for the factory," Zhong says.
About this time, overseas tourists began to trickle into China, and the factory's managers decided to exploit this market by designing collections to appeal to three different cultures: Chinese, Islamic and Western.
The success of this strategy was mixed at best, and under the dictates of supply and demand, the factory was forced to slash its production. By 2002, when the factory turned into a limited company, the work force had been reduced to 800, 60 percent fewer than in its heyday.
Ten years later, the factory soldiers on, but the logistics of production and the limited market produce an equation that is a constant, sobering reminder to those in the business: in the 21st century this 600-year-old craft must earn its keep.
The complicated production process of five steps puts a heavy premium on time and patience, two months being needed to turn out one of the more commonly sized pieces. Something larger and more complicated can eat up half a year.
Ten years later, too, the 800 staff of 2002 have dwindled to just 300, predominantly women, as more and more of the older craftsmen and craftswomen have retired. Into their retirement they have taken hundreds of years of skill, replaced by recruits to the craft who have everything to learn. In the past 10 years there have been little more than two dozen of them.
Despite those bleak figures, there is reason to believe the craft's days are far from over. In 2006, in an effort to protect the craft, enamel was named as a China National Non-Material Cultural Heritage, helping to increase demand.
Those who run the factory are also showing nimbleness in reacting to market demand. The factory has expanded its operations and now creates interior decorations, builds enamel landscapes and produces wares that can be used in the home.
"In recent years we have thought about how people can use these products in their daily lives," Zhong says. "So we design products that people may want to give their friends as wedding gifts."
Works are also being produced that give the craft much needed public exposure. For example, the factory produced an enamel decoration for Beijing International Airport and a large fountain basin at Kuntai Royal Hotel in Beijing.
When Huaxi village, in Jiangsu province, celebrated its 50th anniversary last year it ordered a 1.8-meter-tall enamel gourd statue and a 1.8-meter-diameter fountain basin.
The factory has also used cloisonne techniques to make packaging for products such as liquor and tea.
Zhong has three students born in the late 1970s and early 1980s, who graduated from Beijing Institute of Fashion Technology and Capital Normal University, and who are injecting new blood into the craft.
Their works and pieces have the characteristics of modern art, giving them greater appeal to young people, Zhong says.
The interest that rich Chinese have shown in recent years in investing in art, old and modern, has also broadened the factory's scope for sales.
"At weekends many people drive out to our factory," Zhong says.
Such sales can be lucrative, as evidenced by the prices for pieces by the late Qian Meihua, the factory's first chief engineer. Works that were fetching 4,000 yuan ($630; 510 euros) four years ago are now fetching more than 10,000 yuan, Zhong says.
The products are targeted at three groups of people - those who give them as presents, investors and tourists - and prices range from 2,000 yuan for smaller pieces to more than 100,000 yuan for bigger ones.
However, as some masterpieces are popular among investors, copycats have appeared, and since 2010 the factory has been lodging patent applications for pieces regarded as masterpieces.
In a further sign that the factory has become a fully fledged member of the mercantile age, it puts out pamphlets vaunting its works and puts its wares on display at many traditional arts and crafts exhibitions. Last month it opened a museum on the third floor of the factory.
Sales have grown respectably in recent years, reaching 28 million yuan in 2010 and 30 million yuan last year.
"As we strive to meet changing market demand and more people become more interested in the craft, I think it has a better future," Zhong says.
yangyangs@chinadaily.com.cn
(China Daily 07/20/2012 page19)
Today's Top News
- China's system contributes beyond nation
- Xi's article on unity, hard work to be published
- Xi urges full, rigorous CPC self-governance
- Grassroots Party units continue to play key role
- Global investors double down on Chinese assets
- FM's visit to Europe seen as boosting ties