Chinese solutions break new ground
Updated: 2018-10-23 07:45
By He Shusi in Zhuhai, Guangdong(HK Edition)
|
|||||||||
The island and tunnel project of the Hong Kong-Zhuhai-Macao Bridge (HZMB) has provided the world's civil engineering industry with precious experience and broken the stereotypes of Chinese construction, said major engineers on the project.
The project was conducted offshore in the middle of the Pearl River Delta with no land support. To make the process easier, the team led by chief engineer Lin Ming built a prefabrication factory to manufacture tunnel elements on an island nearby, which largely accelerated the efficiency and minimized the effects of unpredictable weather in the Pearl River Delta.
Deputy chief engineer Dong Zheng said the 560,000-square-meter prefabrication factory is the largest and most advanced of its kind in the world.
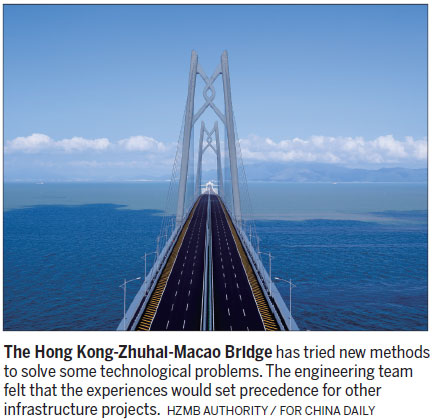
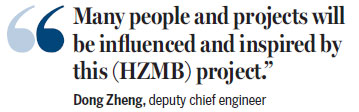
Unlike traditional civil engineering projects that produce reinforced concrete on-site, Dong, who was in charge of managing the factory, said flow line production in the prefabrication factory guaranteed high-quality concrete for each tunnel element, due to its stable temperature and humidity.
"It is the world's only immersed tunnel that doesn't leak water," Dong said with pride.
While ensuring quality, Dong's team also paid great attention to the management of workers in the factory. In civil engineering, he said, the management of people is even more difficult than that of technology.
Dong said his team applied various automation and assembly techniques to minimize the use of manpower, liberating workers from repetitive and tedious work so they could focus on more intelligence-required tasks. He believes this is a development trend that will be used more in future.
"It is of great significance for promoting the concept of large-scale factorization It's a typical example of green development, for higher production efficiency, higher quality, and it is more environmentally friendly than on-site manufacture," Dong said.
"Many people and projects will be influenced and inspired by this (HZMB) project."
After being prefabricated in the factory, all 33 tunnel elements were floated to the installation site. Wang Qiang, also a deputy chief engineer on the project, was a supervisor for the joining and installation of the tunnel elements.
Each element is 180 meters long and weighs about 80,000 tons on average - the largest volume of any of the world's offshore immersed tunnels. "It's like 33 60-floor towers lying on the seabed," Wang said.
It was extremely challenging to limit the errors of installation while manipulating objects weighing that much undersea, he said.
Acknowledging the risks of installing tunnel elements with the complicated geographical conditions in the Pearl River Delta, Wang said he has no regrets participating in the project.
"The island and tunnel project has the highest overall engineering level in the industry," he said.
"The leading role this project plays in the civil engineering industry, I think, is very obvious and strong as it breaks people's stereotypes of traditional construction. The installation of tunnel elements was finished by managing in the control room rather than dealing with rebar (steel rods) and concrete on-site," Wang said.
"The delicate and informationized operations were all supported by data, which is a qualitative leap. I think this represents a trend in the industry - more human-based and more intelligent, which I feel will lead to evolvement gradually," he added.
heshusi@chinadailyhk.com
(HK Edition 10/23/2018 page11)