Technician calls for training help
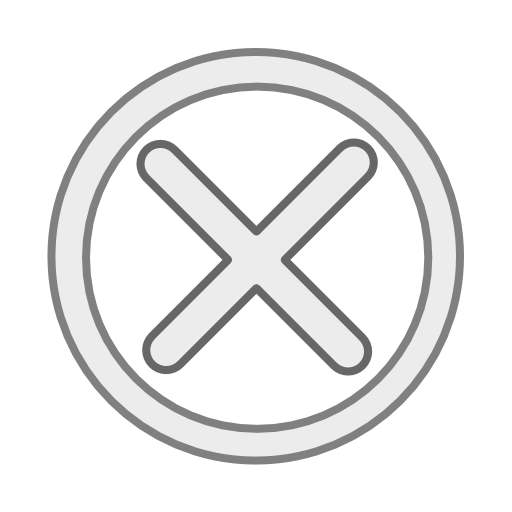
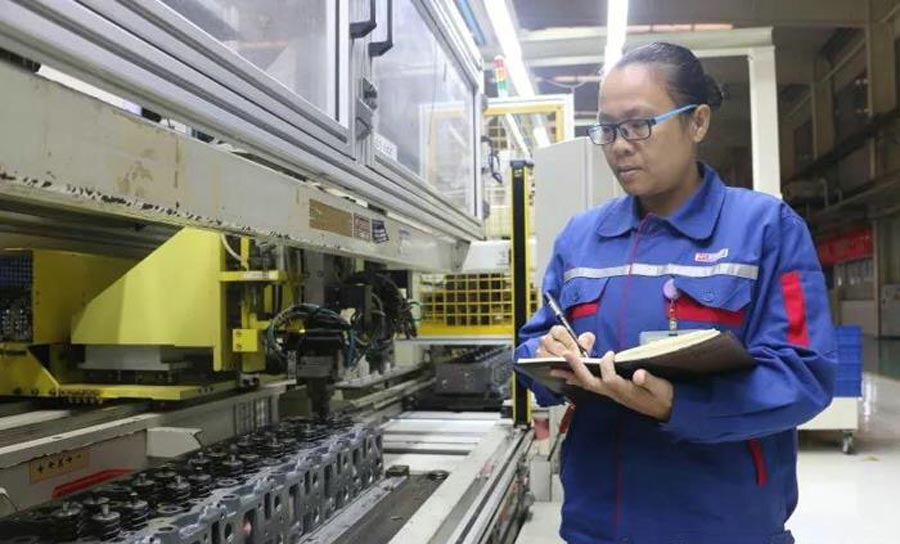
NPC deputy sees benefit for blue-collar workers in occupational standards, incentives
As a technician working on internal combustion engines for more than 20 years, Xu Yanni has suggested the government cultivate more high-level workers by releasing occupational standards and encouraging manufacturing enterprises to train employees.
"The manufacturing sector plays a vital role in the national economy," said Xu, a deputy to the National People's Congress from the Guangxi Zhuang autonomous region. "As a manufacturing giant, China has a large number of technicians. So, training is significant in improving the sector."
In July 1994, she was assigned to work for Yuchai Group after graduating from a vocational school. Yuchai, established in 1951 and based in Yulin, is China's largest producer of internal combustion engines, with more than 20,000 employees and assets of 34.4 billion yuan ($5.4 billion).
When talking with other colleagues, the 44-year-old said she realized they needed to be offered encouragement and incentives, such as higher incomes and more respect.
For more than two decades, Xu has been learning and training others in internal combustion engine testing.
"Assembling and testing engines is boring, and the standards for technicians are high. I believed I could work as well as others," she said.
As an amateur, she always turned to books and more experienced workers for help finding solutions to problems.
"My experience shows the importance of professional training. Each year, the technicians association in Yuchai invests more than 2 million yuan to promote training, which is vital for blue-collar workers," Xu said.
The Government Work Report, delivered by Premier Li Keqiang on March 5, said enterprises will receive support to raise technicians' incomes and provide more incentives to high-level workers.
Xu also suggested cooperation between colleges and enterprises should be deepened to ensure qualified professionals are being trained.
In 2015, Xu introduced a new working model that aims to create value by helping her company eliminate waste to reduce logistics costs for assembly lines.
In her model, conveyors are deployed on the production lines to raise productivity by more than 80 percent. This makes workers' jobs easier. More important, the quality of products can be improved.
Xu also focused on improving efficiency. As a result, only 15 percent of new engines are rejected, compared with 35 percent previously. The length of the production cycle has been reduced by 30 percent, and costs have been cut by more than 10 percent.
In the past few years, she has set up two innovation workshops, trained more than 50 technicians and won over 10 national awards for innovation.
The workshops have applied for more than 50 patents.
In 2016, one of her workshops was granted 200,000 yuan in subsidies by the central government, the first such subsidy in Guangxi.
Her ideas have set a great example for other employees, resulting in her winning a national award for model workers.
"I started as an amateur worker after graduation from vocational school and now I'm a leading technician, thanks to my company helping young workers improve their skills," Xu said.