Talk of sweatshops sparks call for industrial streamlining
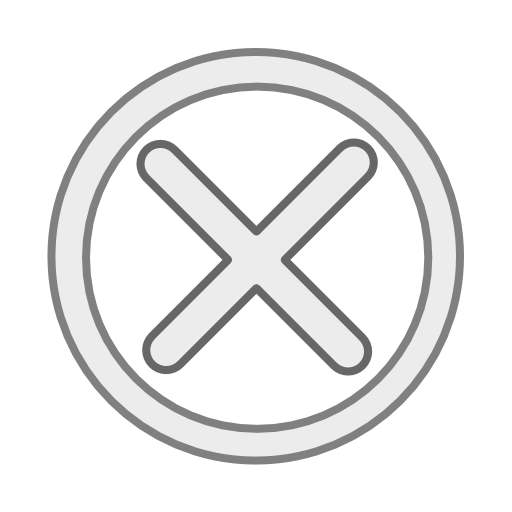
Blue toys in the shape of the mascot for the London 2012 Olympic Games await processing inside the Yancheng Rainbow Arts and Crafts Co Ltd in Dafeng, Jiangsu province. Gao Erqiang / China Daily |
Chinese labor experts and employers have denied that huge numbers of their compatriots still work in sweatshops. Nevertheless, the experts acknowledge that Chinese companies continue to face heavy pressure to maximize their profits.
On Jan 19 and Jan 23 the London tabloid The Sun reported that workers with Yancheng Rainbow Arts and Crafts Co Ltd, which makes Olympic mascot dolls in East China's Jiangsu province, were laboring in sweatshop conditions.
The Sun said those employed in the factory were forced to work 358 hours a month to earn 93 pounds, or about 930 yuan ($148, 111 euros).
"The Chinese workers quoted by The Sun as working for the factory did not even exist," said Gu Feng, chairman of the board of Yancheng, saying a worker interviewed by the radio station Voice of America earlier fabricated the story to tarnish the factory's reputation in retribution for his dismissal.
The US Government Accountability Office has defined a sweatshop as conditions in which an employer violates more than one federal or state labor law governing minimum wages and overtime, child labor, industrial outwork, occupational safety and health, worker's compensation or industrial regulations.
"But in the past two decades Chinese migrant workers have made money and built their houses back home by working on manufacturing lines," said Wu Yaowu of the Institute of Population and Labor Economics of the Chinese Academy of Social Sciences in Beijing.
"Thus, Chinese manufacturers are definitely not sweatshops."
Wu said many Chinese research institutions including the academy had done surveys on migrant workers' pay over the past 15 years. The studies showed that a decade ago a migrant labor's average pay was only 600 yuan a month.
From 2003 the increasing shortage of workers had forced employees to raise pay and improve working conditions. By the end of 2010 the average migrant worker's monthly pay had reached 2,000 yuan.
"With the economic development of the past 30 years, standards of living in the countryside have improved a lot. If factory working conditions are not good enough, it's very hard for owners to recruit sufficient workers."
In 2009 about 75 percent of more than 2,000 factories that were surveyed by the Ministry of Labor and Social Security were short of labor.
China's coastal cities have a shortfall of an estimated 10 million workers, as migrant workers opt to stay in the interior cities where costs are lower, Forbes reported in late December.
It has been widely reported that a shortage of labor has become a challenge for US companies with business in China.
"Our government has been working very hard to protect workers' rights and benefits by launching various laws and policies," Wu said.
"Nowadays not only is the payment of workers guaranteed, but also basic social welfare."
On Feb 8 the central government published details of a national employment promotion plan that aims to raise the minimum wage at least 13 percent each year from 2011 to 2015.
Between 2006 and 2010 the minimum wage rose by an average 12.5 percent a year, and the plan issued by the State Council, China's cabinet, stipulates that the minimum wage should be lifted to at least 40 percent of the average citizen's salary by 2015.
Lou Zhongping, a factory owner in Yiwu, the sprawling commodities trading center in East China's Zhejiang province, has experienced the big changes in workers' demands over the past 20 years.
Rising labor costs have taken a big bite out of factory income, increasing the pressure on manufacturers to find ways to bolster their profits.
Lou, whose company, Soton Straw, is said to be the world's biggest straw maker, announced a 12 percent increase in average pay this month, equivalent to about one third of his total income last year, he said, and bumping up the lowest wage in his factory to above 3,000 yuan.
In order to attract enough workers, Soton has overhauled workers' living conditions, building dormitories in 2008 with four bunk beds in each room.
A couple of sets of body-building apparatus outside the factory are aimed at giving the workers the opportunity for physical exercise.
Lou said the improved conditions had helped little in solving the company's labor shortage or in improving its income.
"The company's profit increased just 5 percent last year, much lower than the 8 percent we achieved the year before, but increasing pay is the key to attracting labor. I am not sure if it's the right thing to do, but I have to do it."
Soton has introduced two mechanized manufacturing lines since 2006. But Lou reckons there is still a 10 percent labor shortage.
Zhang Yi, deputy director of the Research Center for Labor and Social Security, said Chinese manufacturers still needed to improve their operations. "The central government has pleaded for technology and industries to be upgraded for a few years, but our companies haven't done much," China News Service quoted Zhang as saying.
Manufacturing accounts for a large share of secondary industry in East China, Zhang said, and most manufacturing businesses still belong to the low end of the industrial chain.
"Industrial upgrading and modernizing the production line to improve the quality of Chinese manufacturing lines is the solution," Zhang said.
(China Daily 02/10/2012 page3)
Today's Top News
- Unified national market a new growth launchpad
- US deal a structural challenge for Japan
- Industrial prowess of China a subject of serious study
- US new tariffs 'unfair': Experts
- NDRC recalibrating steps to drive growth, boost demand
- Wartime hero's legacy fortifies Sino-UK bond