The time and effort behind a work of art
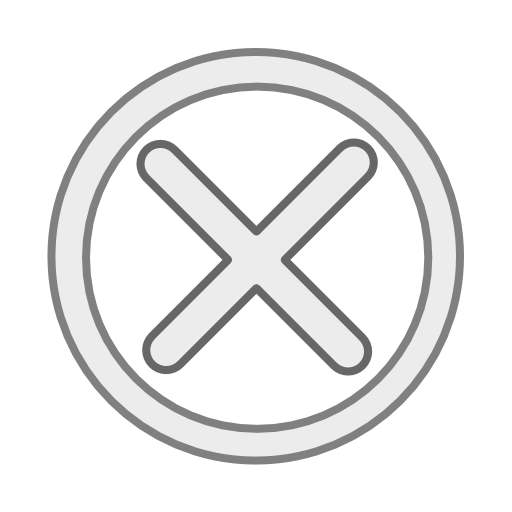
The art of making violins dates back to 16th-century Italy and is a relatively new trade in China. Even though it is a young industry for them, Chinese craftsman are making violins that are up to international standards, with Chinese winning international violin-making competitions in the United States and Italy.
Modern violins originally introduced in China during European colonialism started being produced in the country during the "cultural revolution" (1966-76). Chairman Mao Zedong decided violins were revolutionary instruments and told State-owned enterprises to make them.
International award winning luthier Zhu Mingjiang from Nobel Heart Violins Ltd says making a great violin requires skill and good materials.
"To make a great violin, it takes great technique and ingredients," Zhu says. "European wood is often drier than domestic wood and is great for making violins because it prevents distortion and creates crisper and clearer sounds."
Chinese-made violins often use wood taken from Yunnan and Sichuan provinces as well as the Xinjiang Uygur autonomous region, whereas European violin makers favor wood from the Alps and Bosnia.
According to Zhou Qian, another Chinese violin maker, Chinese wood is often less reflexive with sound.
"Chinese wood is often less 'flexible' than European wood," Zhou says.
"Most of the European brands use wood from the Alps and they produce a finer sound than Chinese violins."
Zhu and Zhou also say modern wood has only been dried for decades and cannot compare with older wood dried for centuries.
But the wood is just the beginning. After the materials have been cut, carved and assembled, there are two more integral parts to making the violin: Design and painting.
One can begin to expect what kind of sound the instrument will produce through the design of the violin, Zhu says. One can decide to make a violin from scratch and use personal designs, or design one following European classics. Master luthiers such as Zhu and Zhou say that the thickness of the backboard and front board is very important and will affect the sound of the instrument.
The painting comes next. The paint used on a violin is very important and many have speculated that apart from the wood that he used, the paint mix was what made Antonio Stradivari one of the greatest luthiers of all time.
Many violin makers spend days toiling over the special blend of oils and paints used to color their creations, to produce something that is audibly and aesthetically pleasing.
"The real luthiers make their own paints, unlike many other who take the easy way out by buying premade paint and then altering it to their liking," Zhu says. "I personally use seven to 10 different ingredients to make my paint. It takes about 80 hours for it to mix right, then I add it to another batch of paint before it's ready."
The whole process of making a single violin can take more than a month. The layered painting is the longest part of the process, but to Zhu and Zhou, the time and the effort taken to create these instruments of art are well worth it.
Today's Top News
- Vast gap has to be bridged for peace to arrive in Europe
- AI powering China's industrial evolution
- Tech innovation propels nation's industrial future
- Chengdu World Games concludes amid wide acclaim
- Trump, Putin say Alaska meeting 'constructive'
- China, India to start new round of consultations